Polylactic Acid (PLA) Plastic
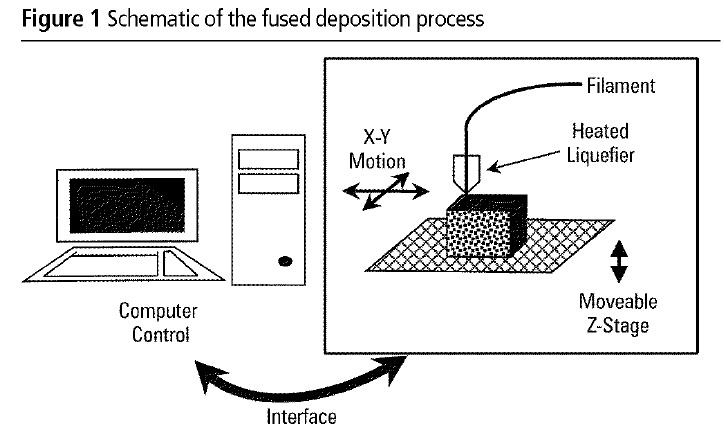
Fused Deposition Modeling (FDM) is a widely used additive manufacturing (AM) technology that involves the creation of three-dimensional objects by melting and extruding a thermoplastic filament layer by layer. It is also known as Fused Filament Fabrication (FFF) or material extrusion. Examples of 3D printers that use FDM technology are the Cube, the Mojo, the Buccaneer®, and the MakerBot Replicator 2X.
FDM was first patented in 1989 by S. Scott Crump, co-founder of Stratasys Inc., and has since been used extensively in various industries such as automotive, aerospace, healthcare, education, and more. It is a cost-effective, versatile, and user-friendly technology that has revolutionized the manufacturing industry.
Examples of 3D Printing using FDM
Fused Deposition Modeling (FDM) is a popular type of 3D printing technology. Here are some examples of objects that can be 3D printed using FDM:
Large-Sized 3D Printing Examples:
Large characters: FDM 3D printing can be used to create large characters and props for events or cosplay, such as life-size characters from popular movies or TV shows. Learn more about 3D Printed Characters.
Industrial models: FDM 3D printing can be used to create scaled-down models of industrial machinery or equipment to test and showcase functionality. Learn more about 3D Printed Industrial Models.
Architectural models: FDM 3D printing can be used to create accurate and detailed models of buildings or structures for architectural firms, construction companies, or real estate developers. Learn more about 3D Printed Architectural Models.
Topographic maps: FDM 3D printing can be used to create 3D topographic maps that show the contours and elevations of an area, which can be useful for geological surveys, urban planning, or environmental studies. Learn more about 3D Printed Topographical Maps.
Video game models: FDM 3D printing can be used to create replicas of video game characters or props, which can be sold as collectibles or used as cosplay props. Learn more about 3D Printed Video Game Models.
Small-Sized 3D Printing Examples:
Phone cases: Custom phone cases can be easily 3D printed using FDM.
Toys: Kids can design and 3D print their own toys such as action figures or cars.
Household items: FDM 3D printers can be used to make household items like kitchen utensils, organizers, and storage containers.
Mechanical parts: FDM can be used to make mechanical parts such as gears and pulleys for various applications.
Customized prosthetics: 3D printing can create customized prosthetics that perfectly fit an individual’s body.
Replacement parts: 3D printing can be used to create replacement parts for broken appliances, machines, or vehicles.
Educational models: Students can design and print 3D models to learn about science, history, and geography.
How Fused Deposition Modeling (FDM) Works
The FDM process involves a few main steps. First, a 3D CAD model of the object to be printed is created using computer-aided design (CAD) software. The model is then sliced into hundreds or thousands of thin layers, each of which is sent to the FDM printer as a set of instructions. The printer then heats a thermoplastic filament, usually made of acrylonitrile-butadiene-styrene (ABS) or polylactic acid (PLA), until it melts and becomes viscous. The melted filament is then extruded through a small nozzle that moves in the X, Y, and Z directions, depositing the plastic layer by layer to create the object.
As each layer is deposited, it quickly solidifies and bonds to the previous layer, creating a strong and durable structure. The printer continues to build up the object layer by layer until it is complete. Once the object is finished, it can be removed from the build platform and any support structures that were used during the printing process can be removed.
Advantages of 3D Printing using FDM
One of the advantages of FDM is its versatility. It can be used to print a wide range of objects, from small prototypes to large-scale production parts. It can also be used with a variety of different thermoplastics, including ABS, PLA, nylon, and more.
Another advantage of FDM is its cost-effectiveness. The materials used in FDM are relatively inexpensive, and the printing process itself is relatively simple and easy to use, which makes it a popular choice for both hobbyists and professionals.
However, FDM does have some limitations. One of the main limitations is its resolution. While FDM can create objects with a high degree of accuracy, it is limited by the size of the nozzle and the thickness of each layer. This can result in visible layer lines on the surface of the object, which can affect its appearance and texture.
Fused Deposition Modeling (FDM) is a widely used additive manufacturing technology that involves the creation of three-dimensional objects by melting and extruding a thermoplastic filament layer by layer. It is versatile, cost-effective, and user-friendly, making it a popular choice for both hobbyists and professionals in various industries. While it does have some limitations, its advantages make it a valuable tool for modern manufacturing.
History of Fused Deposition Modeling (FDM)
Fused Deposition Modeling (FDM) is an additive manufacturing (AM) technology that was first patented in 1989 by S. Scott Crump, co-founder of Stratasys Inc. However, the development of FDM can be traced back to the 1980s when Crump, who was working as an engineer, struggled to create a toy frog for his daughter using traditional manufacturing methods. He realized that he could create the toy by extruding melted plastic through a heated glue gun and onto a platform, layer by layer.
Inspired by this, Crump began to experiment with various thermoplastic materials and nozzles to create 3D objects using a similar process. He eventually developed the FDM process, which involved melting and extruding a thermoplastic filament layer by layer to create a solid object.
In 1991, Stratasys introduced the first commercial FDM printer, the 3D Modeler. This printer was initially used for creating models and prototypes, but its capabilities were quickly recognized by various industries, including automotive, aerospace, and medical, and it began to be used for production parts.
Over the years, FDM technology has evolved, with improvements in the materials used, the accuracy of the printers, and the speed of the printing process. Today, FDM is widely used in various industries and is one of the most popular AM technologies. It has also led to the development of other extrusion-based AM technologies, such as Fused Filament Fabrication (FFF) and Direct Ink Writing (DIW).
In 2012, Stratasys merged with Objet Ltd., a company that specializes in photopolymer-based 3D printing, to become Stratasys Ltd. This merger has allowed Stratasys to expand its range of 3D printing technologies and materials, and it continues to be a leader in the AM industry.
Since its inception, FDM technology has continued to evolve, with advances in both hardware and software. The introduction of new materials and improvements in the printing process have enabled the production of more complex and intricate designs with greater precision and accuracy. For example, Stratasys introduced a new material, FDM Nylon 12CF, which contains carbon fiber to increase its strength and durability. This material is now used in various industries, including aerospace and automotive.
Another major development in FDM technology has been the introduction of multi-material printers, which can print objects using two or more materials simultaneously. This allows for the creation of objects with different properties and characteristics, such as objects with hard and soft components. Multi-material printing is especially useful in the medical industry, where it can be used to create prosthetics and implants that mimic the properties of human tissue.
In recent years, FDM technology has also become more accessible to the general public, with the introduction of affordable desktop printers. This has led to a rise in the maker movement and DIY culture, with hobbyists and enthusiasts using FDM technology to create their own objects and designs.
One of the main challenges facing FDM technology is the issue of surface finish. Due to the layer-by-layer printing process, FDM objects can have visible layer lines and rough surfaces. However, advances in post-processing techniques, such as sanding and polishing, have helped to mitigate this issue.
In conclusion, Fused Deposition Modeling (FDM) technology has come a long way since its inception in the 1980s. It has evolved to become one of the most popular AM technologies, used in various industries for both prototyping and production parts. The introduction of new materials, multi-material printing, and desktop printers has made FDM more accessible to the general public, while advances in post-processing techniques have helped to improve surface finish. As the technology continues to evolve, it is likely that we will see even more advances in FDM technology in the future.
To learn more about the latest in 3D Printing, check out 3D printing.